Why is my AC Compressor not working?
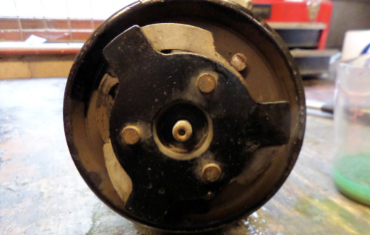
Why is my AC Compressor not working?
Great question. We get this a lot, often when a new one has just been fitted and two weeks later it no longer works, and the customer blames the supplier, when it's the fitting of that compressor that is the issue.
Problems come in a number of ways. From experience we get calls along the lines of:
- It's just stopped work
- It's making a squealing noise
- The belt won't turn on the pulley
- Clutch plate is loose
- Clutch plate/Pulley has siezed up
- and many more....
So what are the causes of these issues? Well a compressor does not just stop working; there is a reason for it, a cause. So you have to identify what has caused this issue before you fit a new compressor. Otherwise, without fixing the cause, you'll have the same problem again. Therefore you should go through a checklist of issues first. Such as has the fuse gone? Does the compressor get power to it when it should have? Is the pressure switch the problem? Does it need oil? Maybe the system is low on refrigerant so does it need a recharge? Eliminate the causes first. There is a useful document from Denso, explaining what to look for and what to check, called Compressor Failure Analysis
Once you've figured out why the old compressor has failed, then the new one must be installed correctly, having first fixed the issues causing the original compressor to stop working. DO NOT simply remove the old compressor, bolt on a new one, regas it and think job done. I guarantee you'll have further problems with the new compressor within weeks doing it like that, as many garages do. That is why compressor warranty terms now state you MUST fit the compressor correctly; more on that later.
We supply with every compressor a fitting guide, along with many other useful documents in the downloads section of our website.
Follow that guide. Make sure you flush out the system, with a flushing solution to remove any residual dirt, oil and other contaminants. If you don't do that any debris in the system is liable to sieze the new compressor very quickly. Make sure you change the drier, and check the expansion valve is clean, if not replace it. All of our compressors come pre-filled with oil, but check it. Add the correct amount of oil for that vehicle. We've a chart on our website showing quantities but if you've not flushed the system out so it's empty and you add more oil you've no idea how much oil in total is there, which then can cause liquid lock, and fail the compressor.
So before fitting a new unit, check why the old one failed first. And before complaining to the supplier the new compressor you had fitted has stopped working, check it was actually fitted properly in the first place. Many garages do not fit them as they should do. The plug the car into a machine, bolt on compressor, regas, job done. Nope. Don't do that. This is why 95% of compressors returned to us under warranty are rejected. They've not been properly fitted. They come back full of debris as the system was not flushed, or too much oil so it's liquid locked (front plate will fail), not enough oil etc.
It's pretty simpe really, find the fault, fix the fault, fit properly.